Gazdaság
Hogyan készülnek a „keréken guruló számítógépek”?
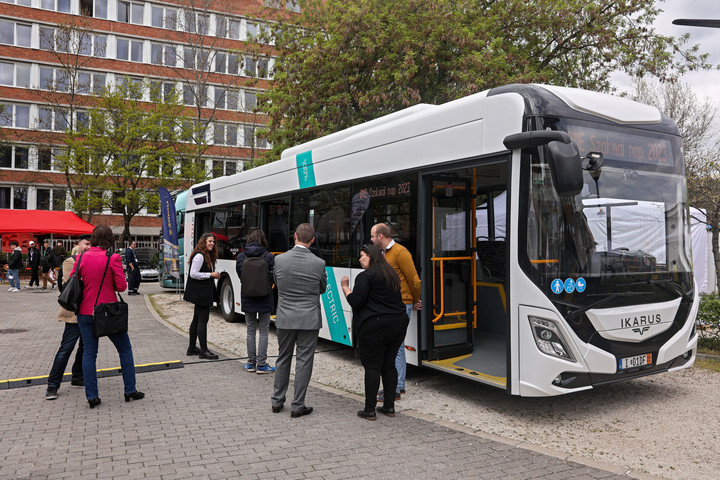
A jövő mérnökei kíváncsian járták körbe a BME szakmai napján az Ikarus büszkeségének számító 120e típusszámú elektromos buszt, amelyből immár egy tucatnyi közlekedik Székesfehérváron. A konstrukció teljes egészében magyar szakemberek munkája: itt tervezték és rakták össze, ők fejlesztették a vezérlő- és biztonsági rendszerét, gyártották a vázat, valamint számos komponensét. A jármű ugyanakkor már külföldön, szélsőséges körülmények között is bizonyított – helytállt az Alpokban épp úgy, mint a parajdi sóbányában.
De hogyan válik egy ötlet valósággá? Somorai Krisztián, az Ikarus Electric Zrt. vezérigazgatója az egyetem nagytermében ebbe nyújtott bepillantást, lépésről lépésre haladva.
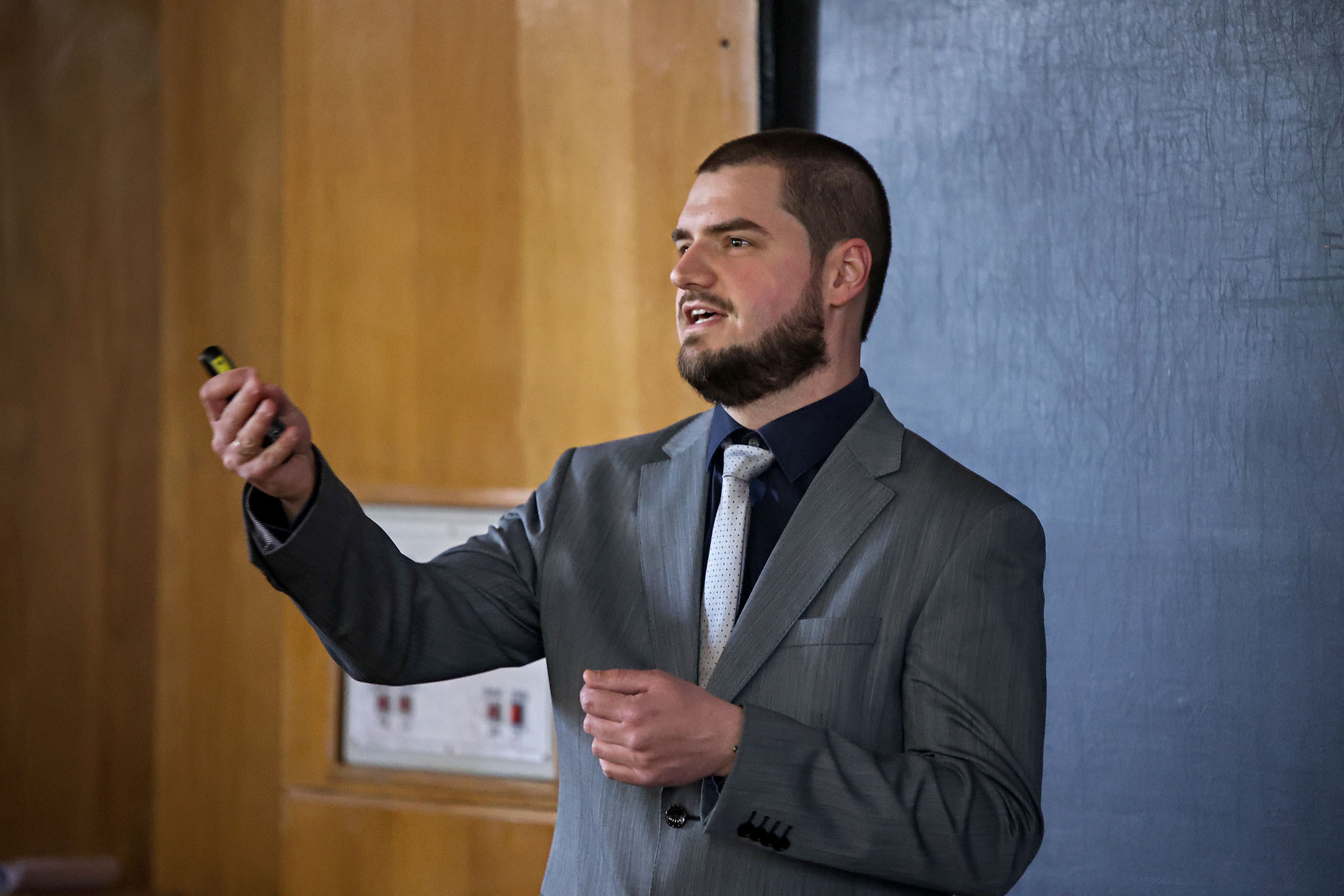
„Az Ikarusnál sokrétű, egyszerre kihívásokkal és örömökkel teli munkát végzünk – kezdte előadását, majd nyomban leszögezte: – egy elektromos busz igen komplex mérnöki rendszer, tulajdonképpen több guruló számítógép együttese, a komputerek szinkronizált együttműködése teszi lehetővé, hogy a jármű elinduljon, megálljon, kanyarodjon, világítson.”
Fehérváron jellemzően városi és elővárosi felhasználásra szánt buszokat gyártanak, bár időnként előfordulnak egyedi igények is. Erre jó példa a MobiMed Bus, amit egészségügyi szolgáltatók számára alkottak meg a covidjárvány idején.
A tervezés folyamán számtalan dologra kell odafigyelni a vevői igényeken túl: vannak nemzeti és nemzetközi szabványok, illetve olyan – kötelező érvényű – nemzeti irányelvek, mint például Németországban a VDV-ajánlások, amelyektől nem lehet eltérni. Ezek, mint Somorai Krisztián szavaiból kiderült, néha egészen abszurdak. Ki gondolná például, hogy adott esetben azon áll vagy bukik egy üzlet, hogy a sofőrnek a jobb vagy a bal kezénél van-e egy adott kapcsoló.
Az élet is gyakran újításokat követel: a covidjárvány alatt kiemelt szemponttá vált, hogy az utastér könnyen fertőtleníthető legyen, ugyanakkor maradjon esztétikus, az ülések, a burkolati elemek pedig finom tapintásúak. Már ennyiből is látszik, mi mindenre oda kell figyelni a kezdetektől fogva, és ez még csak a jéghegy csúcsa. A jármű a típusengedélyét egy apró hiba miatt is elbukhatja, de hogy ez ne történjen meg, az Ikarusnak van egy saját homologizációs mérnöke, akinek csak az a feladata, hogy a tervezés korai fázisától szavatolja az előírásoknak való megfelelőséget.
Gondolatból valóság
Az elhangzottak alapján a buszgyártás leginkább egy nagyzenekar működésére hasonlít. Az Ikarusnál használt tervezői szoftvercsomagot úgy találták ki, hogy mindenki ugyanabban a modellben dolgozhasson; mindenki láthassa, hol tart, mivel foglalkozik éppen a kollégája – hiszen, mint már említettük, számtalan dolgot kell összehangolni, és a gyártási folyamat cseppet sem lineáris. Például a leendő busz 3d-s modelljének megalkotása megelőzi a 2d-s rajzokét, amelyekkel viszont párhuzamosan készül az elektromos dokumentáció.
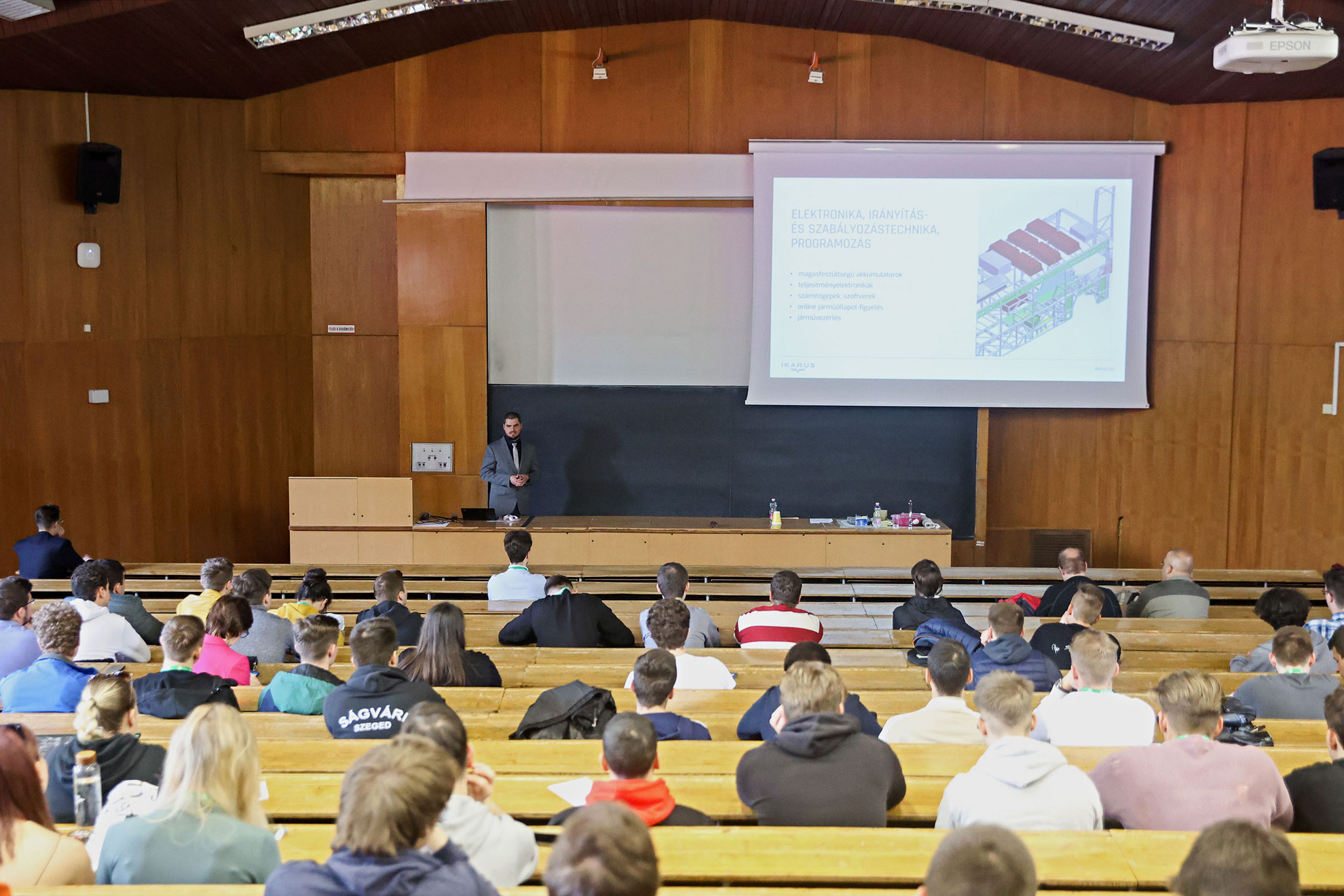
A mérnökök mindent külön-külön papírra vetnek, illetve megterveznek digitálisan. A gyárban aztán a különböző vonalak és jelek fizikai testet öltenek, beépítendő komponenssé állnak össze. Kiemelendő, hogy a tervezés annyira aprólékos, hogy a legutolsó kábelköteg elhelyezkedésére is kiterjed – a vezetékek nem csak úgy futnak a burkolat mögött! „A kábelkötegrajz, a kapcsolási rajz alapján készül, és a saját kábelköteggyárunk ez alapján, ott helyben az Ikarusban gyártja le a kisfeszültségű kábelkötegeket” – jegyezte meg ennek kapcsán Somorai Krisztián, hozzátéve: a szoftverfejlesztés, amiről azt gondolhatnánk, sokadik a sorban, már a váztervezés előtt megkezdődik, mivel annyi mindenre van befolyással.
Ide kívánkozik, hogy a gyengeáramú rendszerek vezérlését, illetve a fedélzeti vezérlő szoftverét is teljes egészében a vállalat készíti és fejleszti. Tehát, amit a sofőr maga előtt, a képernyőn lát, az Ikarus szakemberei munkájának az eredménye. A vezérigazgató röviden bemutatta saját vezetéstámogató rendszerüket is, amit a közelmúltban kezdtek el alkalmazni a városi buszoknál. „A legveszélyesebb manőver haszongépjárműveknél mindig a jobbra kanyarodás, mivel olyankor számottevően megnövekszik a holttér: ilyen esetben például egy kerékpáros könnyen olyan helyzetbe kerülhet, ami a tükörben nem látható. Az ebből adódó baleseteket hivatott a holttérfigyelőnk megakadályozni” – mondta.
Mitől megy, hogyan megy?
Az előadásból az is kiderült, hogy a vállalat különös hangsúlyt fektet a diagnosztikára, az optimalizálásra, és az üzemeltetői tapasztalatokból származó adatok feldolgozásával folyamatosan tökéletesítik a beállításokat. Enélkül nem is lehetne jó buszt gyártani, hiszen a gyártói kínálatból kiválasztani egy akkumulátort csak az első lépés, a megfelelő működéshez és a kívánt teljesítmény eléréséhez számos tesztre, komoly szaktudásra van szükség. Az Ikarusnál ezért a kezdetektől fontosnak tartották, hogy a kondicionálásához szükséges berendezésekkel és kompetenciával egyaránt rendelkezzenek.
„Mi befolyásolja a hatótávot egy elektromos busznál? Ez nem csak azon múlik, hogy mekkora akkupakkot építünk bele. A jármű konstrukciója, a hajtásrendszer, illetve a hajtásvezérlés, a klimatizálás mind közrejátszik. De a forgalomszervezés és a sofőrök vezetési stílusa is kiemelten fontos. Több mint kétszeres szórás tapasztalható fogyasztásban a székesfehérvári flottánál csupán a sofőr vezetési stílusától függően. Ugyanígy számítanak a földrajzi adottságok vagy éppen az időjárási viszonyok” – sorolta a vezérigazgató, aki a buszok felszereltségéről, a „hardware-ről” is elárult egyet s mást.
Többek között azt, hogy az Ikarus a központi motoros kialakítást alkalmazza a kvázi-kerékagymotoros helyett, mivel a központi motorok könnyen szerelhetők, kedvező az árfekvésük, és széles körben hozzáférhetők. Ami az energiatárolót, vagyis az akkumulátort illeti, ezekből háromféle van a piacon. A legnagyobb energiasűrűsége a nikkel-mangán-kobaltosnak (NMC) van, viszont komoly biztonságtechnikai hátránya, hogy képes az öngyulladásra és hevesen ég, ha pedig nem fix hőmérsékleten van tartva, akkor akár egy éjszaka alatt is képes az önkisülésre. Az Ikarus ezt is figyelembe véve a „lítium-vas-foszfát kémiát” (LFP) választotta, mivel tartós, biztonságos – extrém körülmények között sem gyullad ki –, a teljesítménye elfogadható – igaz, kissé időigényes a töltése. A vezérigazgató hozzáfűzte, folyamatban van egy új generációs akkucsomag (a jelenleg alkalmazott pakkok vízhűtéses és kissé emelt kapacitású változatának) integrációja.
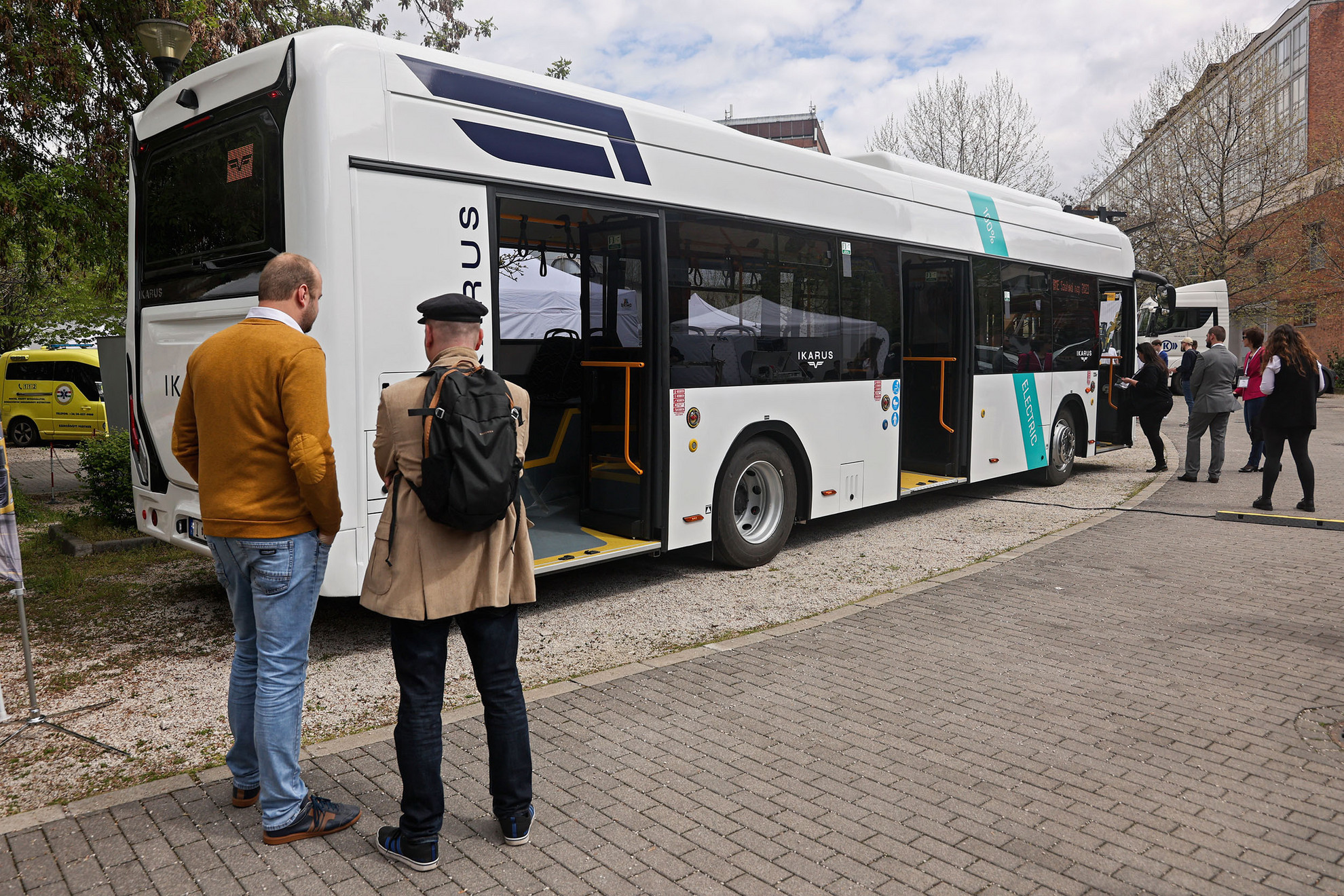
Mindent egybevetve tehát minden fehérvári busz egy hihetetlenül bonyolult, sokrétű munkafolyamat eredménye – és a velejéig magyar. „A tervezést; a szerszámok és a sablonok elkészítésétől a váz- és kábelköteggyártáson át egészen a végső beállításokig, diagnosztikáig mindent az Ikarus csinál. Amit fél éven keresztül rajzolnak a kollégák, az három hónap múlva, néhány száz méterrel arrébb, az üzemben életre kel, és elindul az első tesztekre. Minden pillanat, amikor egy kész busz kigördül a kapunkon, leírhatatlan öröm valamennyiőnk számára” – állapította meg Somorai Krisztián.